By Neeva-Gayle Candelori, Director, Center for the Polyurethanes Industry
For spray polyurethane foam (SPF) contractors, the job isn’t done until the drum is properly disposed. Sure, contractors know that disposal of drums must always proceed in accordance with the foam manufacturer’s instructions, but do they know that since empty drums are potentially hazardous, it’s crucial that they be handled properly by appropriately trained personnel?
Understanding SPF Components
The SPF components are made up of an “A” side — polymeric methylene diphenyl isocyanate, pMDI, or MDI-based diisocyanate — and a “B” side — polyol resin, polyol-based system with smaller amounts of catalyst(s), a blowing agent, flame retardant(s), and a surfactant. These components are typically purchased and shipped as a set or system of two drums, one for the “A” side and one for the “B” side. The drums may be colorcoded red or black for the “A” side, and blue or another color for the “B” side. Each drum contains shipping papers, indicating the required shipping information for that chemical, and any relevant hazard communication labels.
Because most SPF systems are designed to be run at a 1-1 ratio, any components remaining when the job is completed should be in the same ratio. At the end of a job, you should be left with two empty or partially empty drums awaiting disposal. What are you supposed to do with these?
U.S. Regulation of Waste Disposal
The disposal of solid wastes, including those that are deemed hazardous wastes, is regulated in the United States.
SPF contractors disposing of empty or partially empty drums must identify and thoroughly understand the applicable regulations that govern waste disposal.
In the United States, the Environmental Protection Agency’s (EPA) Resource Conservation and Recovery Act (RCRA) is the primary governing federal statute. The EPA promulgates regulations under RCRA, and these regulations impose strict requirements upon hazardous waste generators concerning waste classification, waste accumulation, treatment and disposal, recordkeeping, and emergency preparedness.
States and localities can have additional requirements, so contractors must check and understand federal, state, and local requirements before proceeding with disposal of waste components, foam, or drums. With SPF, there are regulatory distinctions between hazardous and non-hazardous waste.
Always refer to the manufacturer’s material safety data sheet (MSDS) to check each component of your SPF. Handlers of hazardous waste must meet certain regulatory requirements. Generators and transporters must have government-issued identification numbers and comply with other regulations regarding the handling of hazardous waste. Treatment, storage, and disposal facilities must meet even more stringent requirements, and must have a permit to operate.
Wastes that exhibit certain characteristics may be regulated as hazardous under RCRA. A waste may be considered hazardous if it is ignitable (i.e., burns readily), corrosive, reactive (e.g., explosive), or extraction procedure (EP) toxic. Waste may also be considered hazardous if it contains certain amounts of particular chemicals. These are called characteristic wastes, and in addition to these, the EPA has developed a list of over 500 specific hazardous wastes.
In compliance with the testing methods in the EPA’s Code of Federal Regulations (CFR) for the Protection of the Environment, 40 CFR Part 261, neither the “A” side or “B” side, nor any foam products, would typically be expected to possess the characteristics of a hazardous waste. When disposed of in its original purchased form, pMDI is not a listed hazardous waste under RCRA.
Disposal Considerations
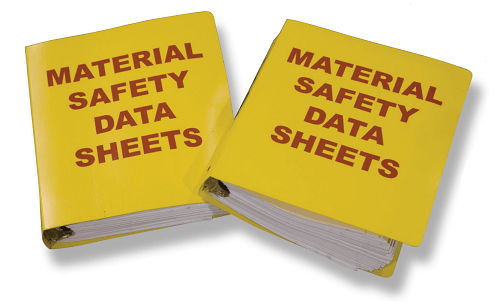
Although the components of SPF are not usually considered hazardous, the disposal of any remaining chemicals needs to be addressed. Again, read the manufacturer’s MSDS instructions to help determine this.
The first step in preparing a drum for disposal should be to consult the manufacturer’s MSDS for specific information on regulatory compliance, safety issues, hazards, spill procedures, and product disposal. Always follow the manufacturer’s MSDS instructions.
The drum is then typically readied for disposal by emptying the drum and removing all labels. A drum is emptied in accordance with federal regulatory requirements under 40 CFR 261.7. This provides that “a container or an inner liner removed from a container that has held any hazardous waste, except a waste that is a compressed gas or that is identified as an acute hazardous waste listed in 261.31, 261.32, or 261.33(e) of this chapter, is empty if: (i) All wastes have been removed that can be removed using the practices commonly employed to remove materials from that type of container, e.g., pouring, pumping, and aspirating, and (ii) No more than 2.5 centimeters (one inch) of residue remain on the bottom of the container or inner liner, or (iii)(A) No more than three percent by weight of the total capacity of the container remains in the container or inner liner if the container is less than or equal to 119 gallons in size; or (B) No more than 0.3 percent by weight of the total capacity of the container remains in the container or inner liner if the container is greater than 119 gallons in size.”
Emptying a drum until it is “drip dry” is generally considered a practice commonly employed to remove materials of this type from a drum. It is important that personnel be properly trained on how to empty pMDI drums and how to decontaminate the empty drums.
Unused pMDI can be reacted with unused polyol to produce foam, and this foam can be disposed of as non-hazardous waste. The remaining pMDI residue, or “A”-side drum, can then be neutralized with an appropriate solution, such as a water and five to 10 percent sodium carbonate mixture, and allowing it to react for a suitable period (e.g., 48 hours). Avoid tightening the bung caps because this neutralization process can cause carbon dioxide gas to generate, which, in a closed container, can cause a violent rupture. After the neutralization has been completed, the rinse water (called rinsate) used to clean the drums is filtered and the neutralization solution is disposed of in accordance with applicable requirements. Check with your local publicly owned waste treatment facility for guidance before discharging any rinsate or neutralization solution into a public sewer system. This contact information should be readily available in a phone book or on the Internet.
Current MSDSs and similar documents should be read and understood before handling the “B” side. If the “B”-side contents are not determined to be hazardous, the drum may be drained and flushed with copious amounts of hot, soapy water. If necessary, rinse a second time with hot water before inverting the rum and letting it dry. Dispose of any material from this process in accordance with federal, state, and local regulations and requirements.
After a drum has been decontaminated, it may be relabeled as decontaminated for subsequent handling.
Used containers may be subject to unauthorized use. Techniques to help avoid unauthorized use include crushing or puncturing the decontaminated and empty drum. Even after a drum is empty, though, heat or sparks can liberate toxic decomposition products, so avoid the use of gas or electric cutters to cut empty drums or to burn empty drums.
Selection of a Receiving Facility for Empty Drums
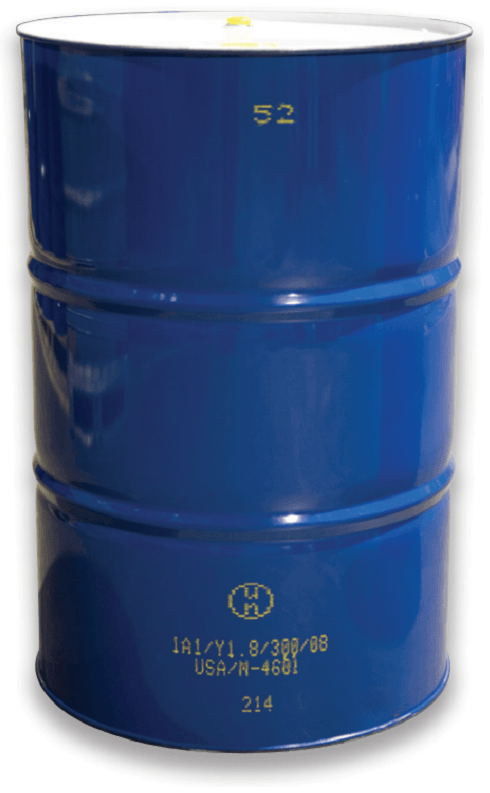
Properly decontaminated empty drums may be shipped to a licensed drum reconditioner, a scrap metal recycler, or an approved landfill. To ensure you’re dealing with well-respected companies, carefully check the reputation of facilities handling empty drums. Reconditioners may require drums to be decontaminated prior to receipt. Because reconditioners use a variety of different techniques to clean drums and to prepare them for reuse, the SPF contractor should consult with the reconditioner before using any drum decontamination procedure. More information on drum reconditioning facilities can be found at www.reusablepackaging.org
In practice, disposal of empty drums into a local municipal solid waste facility (or landfill) is rarely an available option because so many landfills have implemented outright bans on accepting recognizable drums. In some cases, processors may be able to destroy the drums (e.g., by using a drum crusher) and send them to a municipal solid waste facility — if applicable — or to a metal scrap dealer.
Always wear appropriate personal protective equipment (PPE) at all times when handling SPF chemicals and the drums containing these materials. Consult the manufacturer’s MSDS for specific information about PPE. In addition to the suggestions here, all persons involved in the handling and disposal of SPF drums have an independent obligation to ascertain that
their actions are in compliance with current federal, state, and local laws and regulations, and they should consult with legal counsel concerning such matters. It’s up to you to dispose of your drums properly!
For more information about handling and transporting polyurethane, check out the Center for the Polyurethanes Industry of the American Chemistry Council at www.americanchemistry.com
This guidance was prepared by the Center for the Polyurethanes Industry of the American Chemistry Council. It is intended to provide general information to persons who may handle and dispose of spray polyurethane foam drums. The American Chemistry Council makes no warranty or representation, either express or implied, with respect to the accuracy or completeness of the information contained in this article, nor does it assume any liability for any information contained in this article. The discussion in this article is limited in scope and is
not intended to be exhaustive. SF
The Center for the Polyurethanes Industry of the American Chemistry Council promotes the sustainable growth of the polyurethane industry by identifying and managing issues that could impact the industry, in cooperation with user groups. Its members are U.S. producers or distributors of chemicals and equipment used to make polyurethane and manufacturers of polyurethane products. The business of polyurethanes is a $56.1 billion enterprise, supports about 220,000 jobs, and is a key element of the nation’s economy.